Table of contents
Value stream mapping is a Lean management technique that helps companies define and visualize the steps involved in getting a product, service, or value-adding project from ideation to the delivery of value to the end consumer. When performed effectively, value stream mapping can help organizations optimize the flow of value, creating a more efficient, predictable, and agile system.
How to Identify Your Value Streams
View the eBook • How to Identify Your Value StreamsEnterprise Agile Planning Demo
Watch the solution demo • Enterprise Agile Planning Demo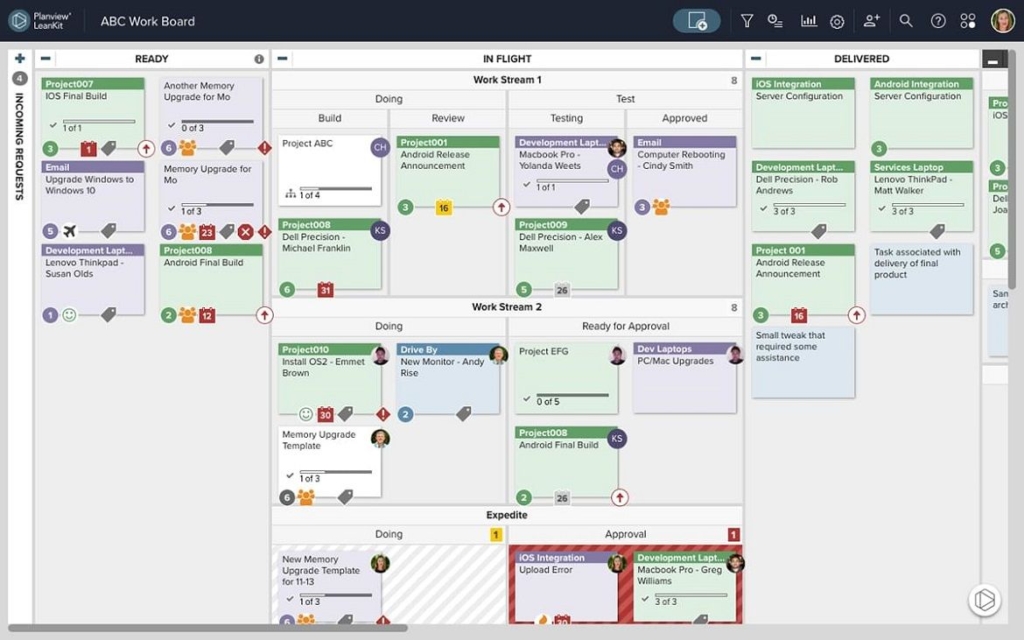
Before we dive into the purpose, benefits, and process of value stream mapping, let’s take a moment to define what exactly we mean by “value stream.” In Lean, value is defined through the eyes of the customer; anything that adds value to the customer is value.
The goal of any Lean organization is to create more value for their customers. Any activity, product, process, or service that does not add value to the customer is considered waste.
In order to create more value (and reduce waste), you must fundamentally understand how value flows through your organization. The way value flows through your organization is called a value stream. It’s the set of actions it takes to turn a customer request into a completed project, product, or service.
In some organizations, there is a single value stream through which all value is created, making it simple to identify and visualize how value flows through the organization. In most organizations, there are several value streams, which might rely on shared processes, competencies, systems, and tools to deliver value.
Understanding exactly how value flows through value streams can get complicated. This is where value stream mapping comes in.
Value | Value Stream | Value Stream Mapping |
---|---|---|
Anything that adds value to the customer–anything for which a customer is willing to pay. | The set of actions an organization takes to deliver value to a customer in the form of a product or service. | The process of visualizing the current state and designing the future state of a value stream to identify areas of improvement. |
Purpose of Value Stream Mapping
There are many reasons that an organization might be driven to undergo a value stream mapping exercise, but the fundamental purpose of this activity is two-fold:
- Identify how value flows through the organization
- (Identify opportunities to) optimize how value flows through the organization
Identify the flow of value
The first purpose of value stream mapping is to help organizations clearly define the flow of value; more specifically, what resources, processes, and systems are involved in the creation of value from beginning to end.
Value stream mapping can help to answer some of those important, big-picture questions, such as:
- What systems, processes, and technologies are involved in creating value for our customers?
- What does it take for us to satisfy a customer need?
- Where do our value streams intersect?
- Are there ways we can streamline our processes to make it easier to satisfy the needs of our customers?
Optimize the whole
The secondary purpose of value stream mapping is to give organizations the information they need to improve.
One of the key principles of Lean is that organizations should strive to optimize the whole. The idea is that an organization should function as a unified, coordinated system, working toward a common goal.
Although this might seem obvious, in many organizations, teams operate in silos, competing against each other for resources. This is one of many ways in which not having a clear understanding of how value flows through an organization can impede an organization’s ability to deliver it. Teams can work independently to become more efficient, but if their improvements have negative impacts on other parts of the organization, then their efforts are in vain.
When organizations conduct a value stream mapping exercise, they shed a light on these competing interests and dependencies and can identify opportunities to improve the value stream so that the entire system can work together more efficiently and effectively.
Current and Future State Value Stream Mapping
Most of what we have discussed about value stream mapping so far is about mapping out the current state of an organization’s value streams. This is a critical step and should be performed first in order to clearly define all the elements that are currently involved in creating value.
However, once you have a clear understanding of your organization’s current state, and you can start to identify opportunities for improvement, you can begin to create a future state value stream map: A projection of how you’d like your value stream to evolve over a fixed period of time. A future state value stream map can serve as a blueprint, helping teams orient around a shared vision of where they want to go.
Value Stream Mapping Applications
Though the origins of value stream mapping are in manufacturing, the application of value stream mapping isn’t limited to the assembly line. Any organization that follows a repeatable process can use value stream mapping to reduce waste and improve value delivery.
Let’s look at how value stream mapping has been applied in manufacturing, where it first originated, as well as knowledge work and software.
Value stream mapping history in Lean manufacturing
Value stream mapping was first utilized by Toyota engineers in the twentieth century. The engineers realized that by improving time between handoffs during the manufacturing process, they could improve productivity and reduce waste.
In manufacturing, these handoffs are fairly simple to visualize because they usually involve the handoff of a tangible deliverable through prescribed stations. This makes it easier to see where bottlenecks are forming and slowing down progress.
If, for example, a problem arises when assembling a car, the line workers can physically see the parts stacking up in a certain part of their process. They can then halt production to solve the problem and get work flowing again. This kind of systems thinking has increased productivity, improved collaboration, and reduced waste in manufacturing for decades.
Another manufacturing use case where value stream mapping would be helpful is for a manufacturer that ships millions of computers to customers around the world. It might make sense to create a value stream map that details the manufacturing process for a low-volume PC to get started.
Once the mapping is complete, teams can focus on reducing waste in the process while looking for ways to add value to the customer, like shortening the overall timeline from customer order to order ship.
After the team completes one or two cycles, they can use those learnings to create value stream maps for other PC product lines: Perhaps a higher-volume product next, followed by the most profitable PC product. With each expansion to additional products, teams are building on work flows they’ve optimized over time.
Value Stream Mapping History in Knowledge Work
Value stream mapping is gaining momentum in knowledge work because it encourages systems thinking, improves collaboration, and increases efficiency.
Much of the waste in knowledge work occurs in the handoffs (or wait time) between team members, not within the steps themselves. Inefficient handoffs in knowledge work may not look like bottlenecks on a car assembly line, but they produce the same effect: Decreased productivity, overwhelmed workers, and lower work quality.
At the organizational and team levels, value stream mapping helps to clarify where handoffs occur to reduce dependencies, improve productivity, and align the efforts of teams.
Benefits of value stream mapping in knowledge work
As in manufacturing, boosting productivity and reducing waste in knowledge work can increase the bottom line. However, the intangible benefits are equally valuable. Value stream mapping in knowledge work can help your teams:
- Practice systems thinking, creating a culture where team members prioritize their activities based on the needs and capacities of the team
- Improve communication, replacing status updates with higher-level discussion that supports key business efforts
- Create guidelines and policies to guide employee behavior even for tacit work, resulting in more effective communication
- Enjoy higher job satisfaction due to more effective collaboration
- Implement and maintain a culture of continuous improvement
Value stream mapping for software development
Software development is a perfect use case for demonstrating the value of value stream mapping. Like manufacturing, software development follows a repeatable process that has distinct handoffs between steps, and continuous delivery requires the collaborative effort of many specialized individuals.
Having a clear, shared understanding of process is invaluable for software development teams. Undergoing a value stream mapping exercise in software development can help teams reduce handoff delays, improve communication, and increase the speed of delivery. It can also help them solidify their Lean process, ensuring a faster, more linear flow of value to the customer.
Software development is an incredibly fast-paced field, where business requirements are constantly shifting based on market demands. The faster teams can deliver testable increments of value, the faster they are able to receive feedback and improve their product. The benefit of value stream mapping for software development is that teams can continue to refine their process, enabling a sustainable, fast pace of value delivery.
Besides process efficiency gains, the other important aspect to value stream mapping is the goal of building self-sufficient teams. Ideally, these teams are capable of doing at least 80% of the work expected of them without additional resources.
Benefits and Challenges of Value Stream Mapping
The use of value stream mapping continues to grow within organizations due to the numerous benefits it provides. One of the core benefits: It helps organizations shift thinking from projects to product delivery.
Ad-hoc projects generally have a defined start and end point; value stream mapping focuses teams on continuous improvement and efficiency.
Value stream mapping helps individuals and teams understand how their work fits into the bigger picture.
Understanding the organization as a system can incentivize teams to prioritize long-term improvements over short-term gains, resulting in better results for the organization.
One additional benefit is that value stream mapping encourages or even requires cross-team collaboration. This often results in more effective, higher-quality team output and more well-rounded team members in terms of arming them with improved skills and capabilities, as well as an increase in the type of workflow experiences in which team members become directly involved.
There are also some challenges with value stream mapping. The first challenge is that it requires organizations to break through the siloed nature of teams. Value stream mapping forces organizations to reach across silos in manufacturing, communications, marketing, product engineering, software development, finance, and more.
An even bigger challenge for organizations is the potential complexity that comes with value stream mapping. Performing it properly can be a time-consuming process, often taking months, and sometimes years, to complete.
Mapping out complex processes that result in delivery to customers often requires input from multiple team members who understand current processes. And often, value stream mapping means getting input from other entities, such as partners, who have a hand in the delivery process. There are ways to mitigate the complexity challenges; some are presented in the Getting Started section below.
Getting Started with Value Stream Mapping
Much of Lean thinking in knowledge work starts with applying value stream mapping to any work where there are repeatable processes. Although the technical value stream mapping definition varies by industry, its primary concepts have moved beyond manufacturing to be an effective tool for improving processes across all business functions.
Waste in knowledge work occurs in the handoffs between team members; by collectively identifying and visualizing these handoffs, teams have more control over how workflows through the value stream. This sort of systems thinking leads to a culture of continuous improvement that makes teams more effective, with less time wasted in status meetings and more time spent making things happen.
As mentioned previously, it makes sense to start with a single value stream where you’ve identified potential for finding and implementing new levels of efficiency that result in delivering higher quality products to customers at a faster rate. From there, you’ll want to design a Kanban board to visualize workflow, measure effectiveness, and identify opportunities for improvement. Initial steps are:
- Map your process to reflect your current state as closely as possible
- Map your process to reflect a future state – where the organization wants to go
- Design your board to capture the right metrics for improvement
- Develop a detailed action plan that attempts to address process gaps or inefficiencies
- Address common glitches such as wait time and hidden work
Remember that value stream mapping is an iterative process that teams will strive to improve over time. Perfection is not the goal; incremental, repeatable improvement is the goal.
The key is to accurately visualize workflows in a way that encourages continuous improvement. Building the right foundation will help you improve both your products and the skills of the team members responsible for delivering them incrementally over time. And many studies have shown that these repeatable, incremental improvements in aggregate can have a profound impact on organizations in the form of shortening product cycles and reducing costs – all while improving quality as well.